涡轮排气颗粒监测
涡轮排气颗粒监测
测量燃气轮机或喷气发动机排气中微粒携带的静电电荷已成功地在航空领域得到应用,作为可能退化的内部“热区域”(摩擦、叶片涂层和热障层的磨损、燃烧室热点、燃烧不当等)的早期故障诊断工具。测量技术通常称为EDMS(发动机退化监测系统)或EEMS(静电发动机监测系统)。
查看更多
查看更多
查看更多
查看更多
查看更多
工作原理和一般考虑因素
ELMO系统是基于对燃气轮机内部部件退化产生并排入尾气的颗粒所携带的静电电荷进行监测。由于燃烧过程中产生的高温和退化现象,这些颗粒被电离。查看更多
硬件配置
除了传感器,ELMO的系统硬件包括相同数量的电荷放大器,一个信号调理单元,一个采集单元和数据处理/显示/存储单元。查看更多
软件配置和数据分析
系统管理软件完全由CESI开发,主要包括在线采集/存储和显示数据程序,软件模块可以相互通讯、并可与远程单元进行通讯,远程单元通过ad hoc开发的接口软件模块连接到网络。CESI提供的软件包括离线数据处理程序。查看更多
在营运的燃气轮机上安装ELMO的系统
在一个新的燃烧室的全尺寸实验台的初步实验,可以评估该方法对颗粒释放的灵敏度,而且确定了可靠的静电电荷在线监测系统的硬件和软件的必要的技术规范。查看更多
结论
测量尾气的静电电荷作为监测工业用燃气轮机内部零件退化的方法的适用性和潜力,已经被一系列演示项目成功验证。查看更多
涡轮排气颗粒静电监测 - 概要
测量燃气轮机或喷气发动机排气中微粒携带的静电电荷已成功地在航空领域得到应用,作为可能退化的内部“热区域”(摩擦、叶片涂层和热障层的磨损、燃烧室热点、燃烧不当等)的早期故障诊断工具。测量技术通常称为EDMS(发动机退化监测系统)或EEMS(静电发动机监测系统)。对于装配了大型排气管、使用不同燃料、和航空发动机运行在不同的操作条件下的工业燃气轮机能否使用这种监测技术需要具体的实验验证和确认。本文介绍了CESI在一个工业燃气轮机大型现场示范项目中收集的数据的综合和最值得注意的经验。我们评估了根据上述方法研制的仪器监测系统对于机器的不同工作条件和各种可能的退化机理的反应和灵敏度。我们进行了一系列的试验,先在一个全尺寸燃烧试验台上试验,然后直接在发电厂里正在运行的不同结构和额定功率的燃气轮机上进行试验,在这里可以将静电电荷测量结果和机器在定期的或发生故障维修时机器的检查结果进行比较。收集的数据证实这种方法的潜在优势在于它对内部部件存在的退化现象的警告比其它传统监测技术早得多,如那些基于振动分析或“气路”性能技术的传统技术。本文还介绍了由CESI开发的性能优越的ELMO(静电监测)系统的硬件和软件,可以用于工业用燃气轮机的连续监测。根据到现在取得的成果来看,定义一些工作后,这个方法可以自动并及时识别这些机器的主要故障和退化。
涡轮排气颗粒静电监测 - 工作原理
ELMO系统是基于对燃气轮机内部部件退化产生并排入尾气的颗粒所携带的静电电荷进行监测。由于燃烧过程中产生的高温和退化现象,这些颗粒被电离。移动电荷产生的静电场力线和排气管壁上安装的一个或多个特殊传感器相互作用,在传感器里感应出相反的电荷,此电荷被检测并转换成信号用来表征颗粒的存在。电荷传感器是能够在高温工作的被动元件,以非侵入性的方式在排气管壁内面对面安装并使用适当的适配器;传感器数量和位置的选择应使完整气路全部可见。图1显示了CESI制造的传感器及安装的适配器。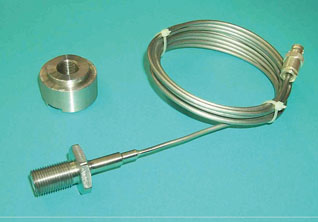
图1 传感器及安装适配器
经验表明,任何燃气轮机在健康状态下都会产生的一个基础水平的静电电荷,电荷水平与工作条件、燃料类型、燃烧稳定性、气候条件和内部部件正常退化和磨损相关。此背景电荷水平用来定义参考“基线”(电荷水平与机器的工作和操作条件成规律)并突出显示由于排气中颗粒异常增加导致的“突起”的电荷水平的“接受阀值”。机器的旋转部件和静止部件的磨擦、轴承密封润滑油的泄漏、燃烧室的热点、叶片涂层和热障层的损失、未完全燃烧的增加、密封磨损、吸入、或气路内组成部件的损失,这些情况都是“碎片”的典型来源,会导致电荷水平的提高。
很显然,并不是所有的颗粒都是与机器故障相关的。例如,在线压气机清洗或激活进气冷却喷雾系统会伴随沉积颗粒沿流路清除,这种情况会造成电荷水平增加但并没有故障。这种类型的事件必须被鉴别出来,以避免误报。相对于传统方法(例如基于机器性能分析或涡轮排气温度分布),在线监测静电电荷方法应用于工业燃气轮机的主要优点是使用有限的传感器(一个或两个),早期预警,直接监控内部组件的退化和实时评估气路状态。
涡轮排气颗粒静电监测 - 硬件配置
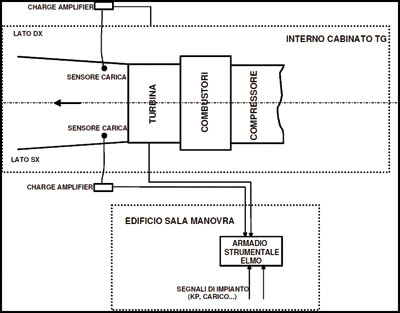
图2 ELMO在工业燃气轮机上的典型安装布局
除了传感器,ELMO的系统硬件包括相同数量的电荷放大器,一个信号调理单元,一个采集单元和数据处理/显示/存储单元。电荷放大器是可变增益放大器,配有带通滤波器,有保护外壳,放置在距离传感器最大5-6米远的地方;这些设备将原始电荷信号转变为一个合适的电压信号,使用同轴电缆传输最大距离可达150至200米。电荷信号和其他发动机工作状态的数据信号(基本上是1个从涡轮转子来的转速信号和涡轮的功率信号)共同进入信号调理单元,该单元装配了optoinsulator模块进行电流绝缘。这些模块与16位DSP采集板单元(最大采集频率高达153.6kHz)相连,采集单元包括8个单端模拟输入通道、8个抗混叠滤波器和8个数字滤波器,软件可编程。板卡插入到一个工业PC的扩展槽,工业PC包含在线数据处理/显示/存储单元。在同一PC上插入额外的板卡就可以同时监测第二个燃气轮机。除了电荷放大器,所有其他ELMO的硬件被安置在一个机柜里,机柜通常放在控制室里。
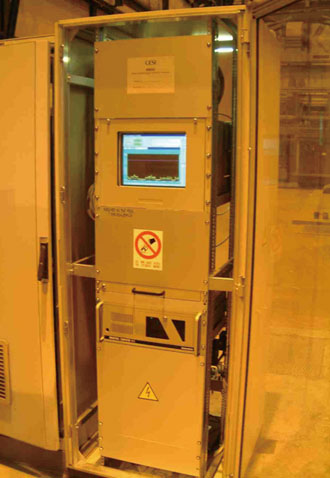
图3 ELMO的机箱
涡轮排气颗粒静电监测 - 软件配置
系统管理软件完全由CESI开发,主要包括在线采集/存储和显示数据程序,软件模块可以相互通讯、并可与远程单元进行通讯,远程单元通过ad hoc开发的接口软件模块连接到网络。CESI提供的软件包括离线数据处理程序。用户界面一部分供专家操作,一部分供工厂操作人员操作。
专家对系统的采集参数(采样,信号灵敏度,报警阀值,数据存储率等)进行设置,定义电荷信号的参考基准, 参考基准以一段时间内获得的足以体现机器的特性的数据分析为基础,设置各种软件之间的通信协议,最后为操作者设置显示页面。如图5所示,与配备了ELMO系统的几台机器相关的数据可在同一显示单元显示。经过合适的过滤和模拟数字转换后,系统对来自电荷放大器的信号的如下基本组成部分进行计算:
活动水平(AL):以pC来表示,代表了电荷信号的高频部分,是尾气中细小颗粒(颗粒直径小于40um)数量的指标;

图4 采集设置窗口
事件率(ER):表示成一个无量纲的百分比,测量在给定时间窗口内超过所设置的阀值的未过滤的原始数据;这部分与任意时间内排气中的大颗粒数(约大于40um)相关;事件按幅度和极性(第一/第二阀值的正极/负极事件)分类。
轴阶次分析:同步或整数倍于燃气轮机转速的电荷水平分量,表示了按照与机器旋转相关频率进行的颗粒释放(例如叶片摩擦)。
这些分量的瞬时值是系统的第一级分析,时间平均值的计算和与机器的操作条件的归一化是第二级的分析。通过在健康的燃气轮机所有可能的不同工作环境采集到的持续而显著的平均数据,就可以使用一个合适的算法来计算出参考“基线”(见图5),代表可接受的统计差异的间隔的电荷信号;当超过阈值,系统自动向设备操作人员发送警报信号(图形或声音)。特别是,报警情况会区分以下两种情况:一种是与机器的内部组件的逐步退化现象相关的信号“漂移”(超过参考基线阈值的基本数量的平均水平),另一种是与突发性和更多意想不到的退化现象(例如叶片损失的极端情况)相关的“单一事件”(超过阈值水平限制的基本数量的瞬时水平)。
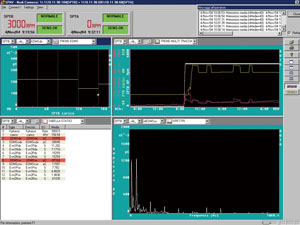
图5 在线数据显示窗口
涡轮排气颗粒静电监测 - 系统实例
在一个新的燃烧室的全尺寸实验台的初步实验,可以评估该方法对颗粒释放的灵敏度,而且确定了可靠的静电电荷在线监测系统的硬件和软件的必要的技术规范。CESI开发了ELMO系统,并持续地在发电厂在役的燃气轮机上进行了验证活动。完成了软件采集、分析和自动存储算法的巩固和完善,以及增加对诊断极为重要的机器事件案例的双重目标后,监测活动已扩展到一些不同尺寸(额定功率45兆瓦至240兆瓦)和不同结构类型(航改和重型燃气轮机)的工业燃气涡轮。比较大的机器(额定功率超过120兆瓦)通常需要安装两个电荷传感器(在紧随涡轮旋转叶片的最后一级的下游部位)以争取对整个气路横向截面都可见:这是由于排气管较大的尺寸以及排气管内存在其它结构部件(热轴承支撑,如图7所示)。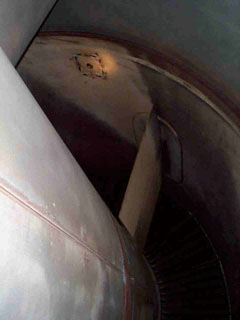
图6 排气管内视图
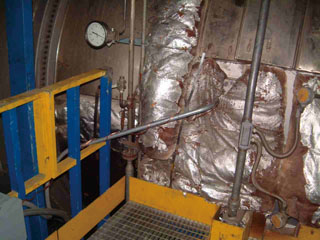
图7 在120兆瓦燃气轮机上安装

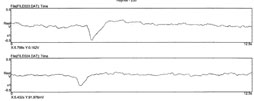
图8 微粒强迫注射及系统响应
首次安装时,要对仪器进行灵敏度评估和标定,使用燃气轮机热部分的常用的不同材料(金属和陶瓷)的粉末(已知重量和成色)用强迫注射的方法进行。(见图8)
扩大到中长期的监测采集来的相当可观数据库,可以验证随实验不断改进和优化的硬件和软件的可靠性和功能性,并实现不同气轮机的个性化。
一般来说,实验已经指出静电电荷背景水平以及电荷水平对不同工作条件的灵敏度会根据机器类型和机器尺寸而改变,并受燃烧参数的设置、燃料成分和气候条件影响。
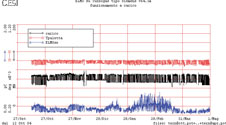
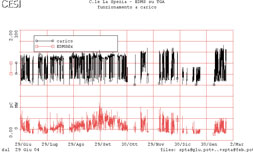
图9 西门子V64.3A(上)和菲亚特701F(下)燃气轮机在额定负荷时计算的活动水平
图9显示,例如,活动水平的时间变化(标记为ELMO sx 或 EDMS dx,dx和sx表明排气管的右侧或左侧),叠加在负荷信号水平上,如在额定功率120兆瓦和240兆瓦的燃气轮机满负荷运转时所监测到一样;活动水平表征了与所设置的燃烧参数相关的“生理”变化。
图10例子显示在额定功率120MW燃气轮机里,由启动“雾化”系统引发的事件率增加(标为CNT-2A)。另一方面,图11显示了在额定功率45MW燃气轮机里,由于燃料混合变化的活动水平增加。以上事例说明电荷水平的可能的和重要的“生理”变化必须被识别并从真正的“病态”中区分出来,以避免误报。
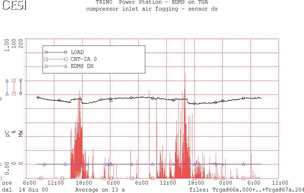
图10 额定功率120兆瓦燃气轮机中“雾化”的影响
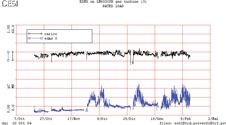
图11 额定功率45兆瓦燃气轮机中混合燃料的变化的影响
在监测期间,系统指出了相当数量“诊断”案例,显示静电电荷方法作为早期异常预警的有效潜力,所有这些都是传统监测技术认为很困难或不能快速做到的。例如,在图12和13比较了同一机器(额定功率240MW燃气轮机)两次不同启动的瞬间电荷信号;在第二次启动中,有一个活动水平的显着增加,特别是在排气管右侧的传感器(图13绿线):轴阶次分析指出是由于一倍(1X)(与转速同步)的部件是影响了整体电荷信号水平增加的基本原因,因此可以诊断为旋转部件在静止部件上的局部摩擦,事后在机器停车后进行维修时的检测确认(图14)此诊断。“局部”摩擦主要存在涡轮第一级右侧的磨瓦,这与安装在排气管的两个方向的两个电荷传感器的响应是一致的。
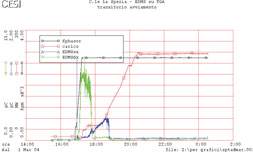
图12 240兆瓦燃气轮机正常启动
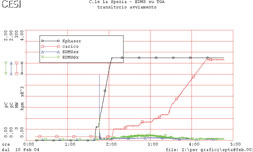
图13 带摩擦的异常启动
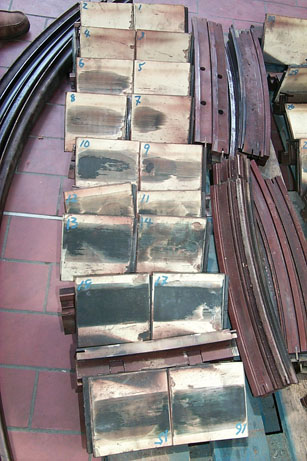
图14 “局部摩擦”的现象
另一个“病态”退化的例子是由ELMO在额定功率45兆瓦燃气轮机上检测出来的,如图15。通常在满负荷时记录到非常低而且持续的活动水平开始增加。根据ELMO系统的警告,工厂操作者计划了在几天后对燃气轮机进行短暂的停车并进行了内窥镜检查,检查发现燃烧室的热障层和涡轮叶片涂层有异常侵蚀的存在。
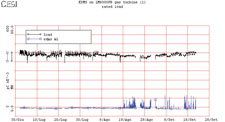
图15 额定功率45兆瓦燃气轮机(型号LM6000PB)的活动水平

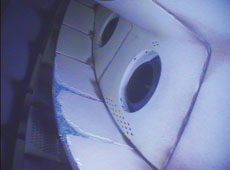
图16 发热元件的内窥镜检查
涡轮排气颗粒静电监测 - 结论
测量尾气的静电电荷作为监测工业用燃气轮机内部零件退化的方法的适用性和潜力,已经被一系列演示项目成功验证,演示项目从实验燃烧室试验台的初步实验开始,一直到在电厂中不同额定功率和结构设计的大量燃气轮机得到应用。